OSHA Compliance for Fire Departments
What You Need to Know About Gas Detection
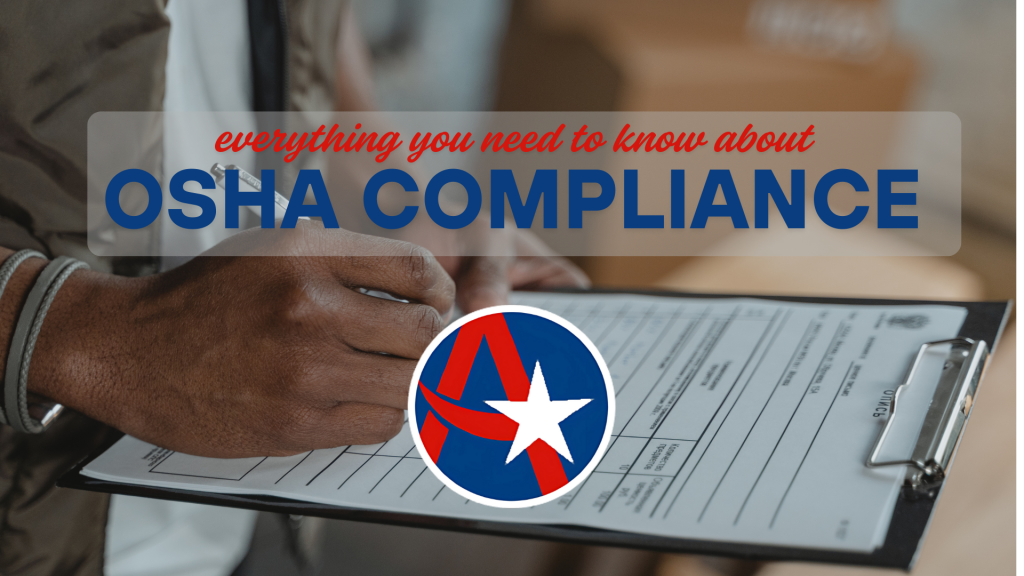
Recent reports confirm that OSHA is increasing enforcement efforts across fire departments in Massachusetts, with a renewed focus on full compliance with workplace safety standards. While many departments have strong safety procedures already in place, new inspections are making it clear: documentation, equipment maintenance, and proactive hazard prevention are now under the microscope.
At Apollo Safety, we understand the unique challenges fire departments face — and we’re here to help you meet these heightened standards head-on.
The Role of Gas Detection in OSHA Compliance
Under OSHA guidelines, fire departments must protect employees (including firefighters, EMTs, and hazmat teams) from known and foreseeable workplace hazards. That includes exposure to hazardous gases such as:
- Carbon monoxide (CO)
- Hydrogen sulfide (H₂S)
- Methane (CH₄)
- Oxygen-deficient environments
Gas detection is not optional — it’s a critical part of hazard mitigation and required under OSHA’s General Duty Clause and several specific standards (including confined space entry requirements).
Key Gas Detection Compliance Steps for Fire Departments
1. Equip Your Teams with Portable Gas Detectors Every firefighter entering an unknown or potentially hazardous environment should carry a calibrated gas detector. This is vital for identifying dangerous atmospheres before exposure occurs.
2. Maintain and Calibrate Equipment Regularly OSHA requires that gas detection equipment be maintained and calibrated according to manufacturer specifications. Failing to properly calibrate or bump test monitors can lead to inaccurate readings — and violations.
3. Document Your Safety Procedures Written protocols for gas detection use, maintenance schedules, and employee training records are essential. In the event of an inspection, departments must be able to show they have a clear, enforced gas detection policy.
4. Train Your Personnel All firefighters must be trained on proper use of gas detection equipment, understanding alarm signals, and emergency response actions. Refresher training is recommended at least annually.
5. Work with Experts Choosing the right equipment, setting up maintenance programs, and ensuring documentation is inspection-ready can be complex. Partnering with a gas detection expert ensures your department stays ahead of OSHA requirements.
How Apollo Safety Can Help
Apollo Safety has been working with fire departments across New England for over 30 years, providing:
- Portable and fixed gas detection solutions
- Calibration services and Peace of Mind maintenance agreements
- Equipment training and compliance support
- Fastest turnaround times in the industry
We understand the urgency — and the stakes — of keeping your crew protected and compliant.
Concerned about your current gas detection program? Want to make sure you’re ready for an OSHA inspection?
Contact Apollo Safety today to speak with a gas detection expert. 📞 800-813-5408 | 📧 sales@apollosafety.com
Let’s work together to protect the protectors — and keep your department ready for whatever comes next.